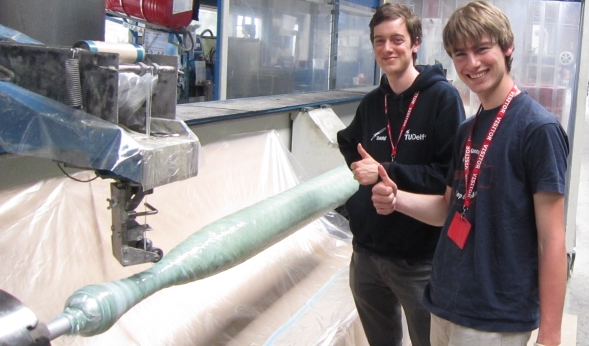
DARE is proud to announce that in cooperation with Futura Composites the glass fiber nosecone and upper body tube of the Stratos II project have been produced. The body tube and nosecone are critical parts of the capsule. They carry all the structural loads that the capsule will experience during flight.
During the past few months a structural analysis of the fiberglass skin was executed. Together with Advanced Lightweight Engineering (ALE), an appropriate lay-up design was designed. After the lay-up design and the design of the mold was discussed with Futura Composites, the capsule team started with the production of the mold, which was made out of PUR foam, aluminum and several layers of epoxy.
After a weekend of sanding and waxing, the team went to Futura Composites. There the specific lay-up design was filament wound around the mold. Subsequently the component was cured for a long period at a high temperature. Finally the product was lathed such that the nosecone and body tube obtained a smooth outer surface of the desired shape The surface was then coated with a thin film of flame retardant epoxy.
To allow for radio communication with the ground station, including live video footage, the body tube and nosecone had to be radio-transparent. This and the lightweight characteristics of glass fber were the main reasons why we opted for glass fiber.