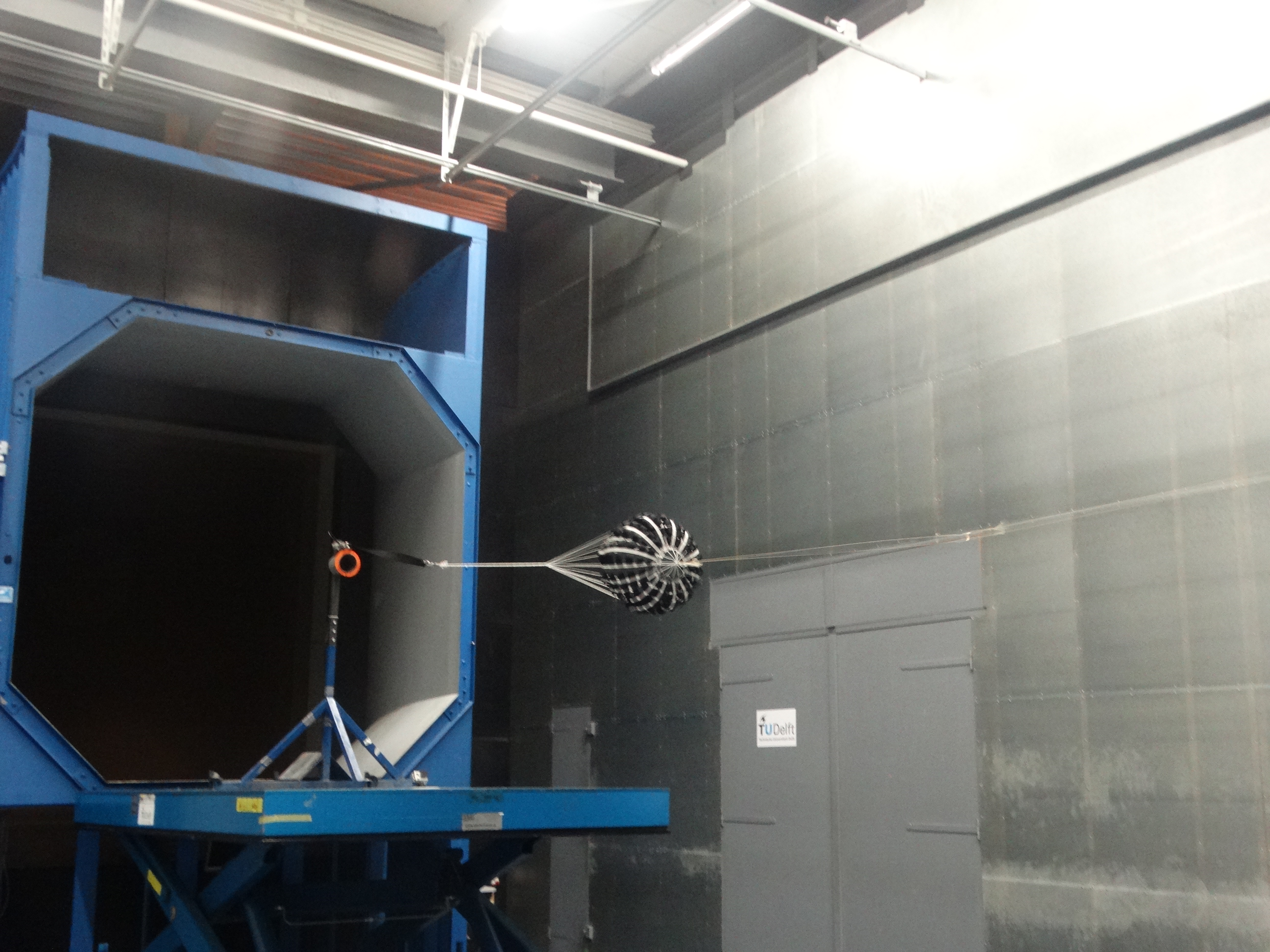
It has been a while, but on January 3rd, 2017 the recovery team, with help of other DARE members, found themselves back in the Open Jet Facility (OJF) to test several new parachutes again. In the week before the holiday, as well as on the holiday itself, people had worked hard to complete all the preparations necessary for this test day. The aim of the day was to find an improved design for the main parachute and a proper design of the drogue parachute.
During the previous wind tunnel test it was observed that the drogue parachute rotated which led to it imploding after a brief period of time. After careful analysis it was though that manufacturing issues were the main problem as well as the ratio of vertical and horizontal ribbons. These issues were fixed for this test by using different size ribbons and a much more streamlined production processes. After a quick set-up on the test day itself, this new and improved drogue was the first parachute to be tested and it preformed as expected, hanging completely stationary in the flow without any rotations. Later repetitions of this test provided the team with the same results confirming that this new drogue was flight worthy.
From the previous test day it was concluded that only a cross parachute with ends attached was stable under the condition and speeds that were considered. The parachute was made by stitching two rectangular pieces of fabric together. The ratio between length and width of this rectangle was 0.33. In order to improve the efficiency of this type of parachute, this ratio was adapted for this test series to create a larger surface area in the middle (more drag) while reducing the size of the sides (less stability). The aim of these tests was to find the optimum value at which the parachute can still remain stable with the largest effective surface area.
Three additional parachutes were produced for this goal with the ratios 0.5, 0.6 and 0.7 respectively. Each of them was tested multiples times at different wind speeds but all of those parachutes proved to be unstable from the instance of deployment onward. It turns out that the team had already reached this ‘stability limit’ with the initial parachute from the first test series without having realized it yet. When this was discovered more test were conducted with the initial parachutes of ratio 0.33 to try and understand it behavior even better compared to last time.
An important area of focus for the day was to limit the initial shock load when deploying the parachute. The slider had already provided promising results in the first wind tunnel tests. In addition an elastic shock cord was tested in order to prolong the time it takes from the load to occur. The data analysis after the tests showed that this shock cord was able to remove about 40% of the shock load. The slider however was able to complete remove the shock load on its own, which made the shock cord obsolete.
The last part of the day was spent on trying to limit the rotation of the parachute, since this twisted up the wires, eventually leading to the parachute collapsing. It was realized that the lines were suspended to close to each other on the metal links that were being used. An improvised method was though off to separate those wire, consisting of a coffee cup and duct tape. This solution proved extremely effective in preventing the lines from twisting and thus a similar, but more advanced and detailed design will be used on Stratos and Aether to prevent this issue from occurring.
This test day was very successful since it provided evidence that the new drogue design produces a parachute that is capable of flight without problem. Furthermore the limit of the main parachute was discovered (by accident already of the initial test) and the shock reduction systems were capable of completely removing the shock load. These will results will be implemented in the design for the Stratos recovery system, to make this system as reliable as possible.