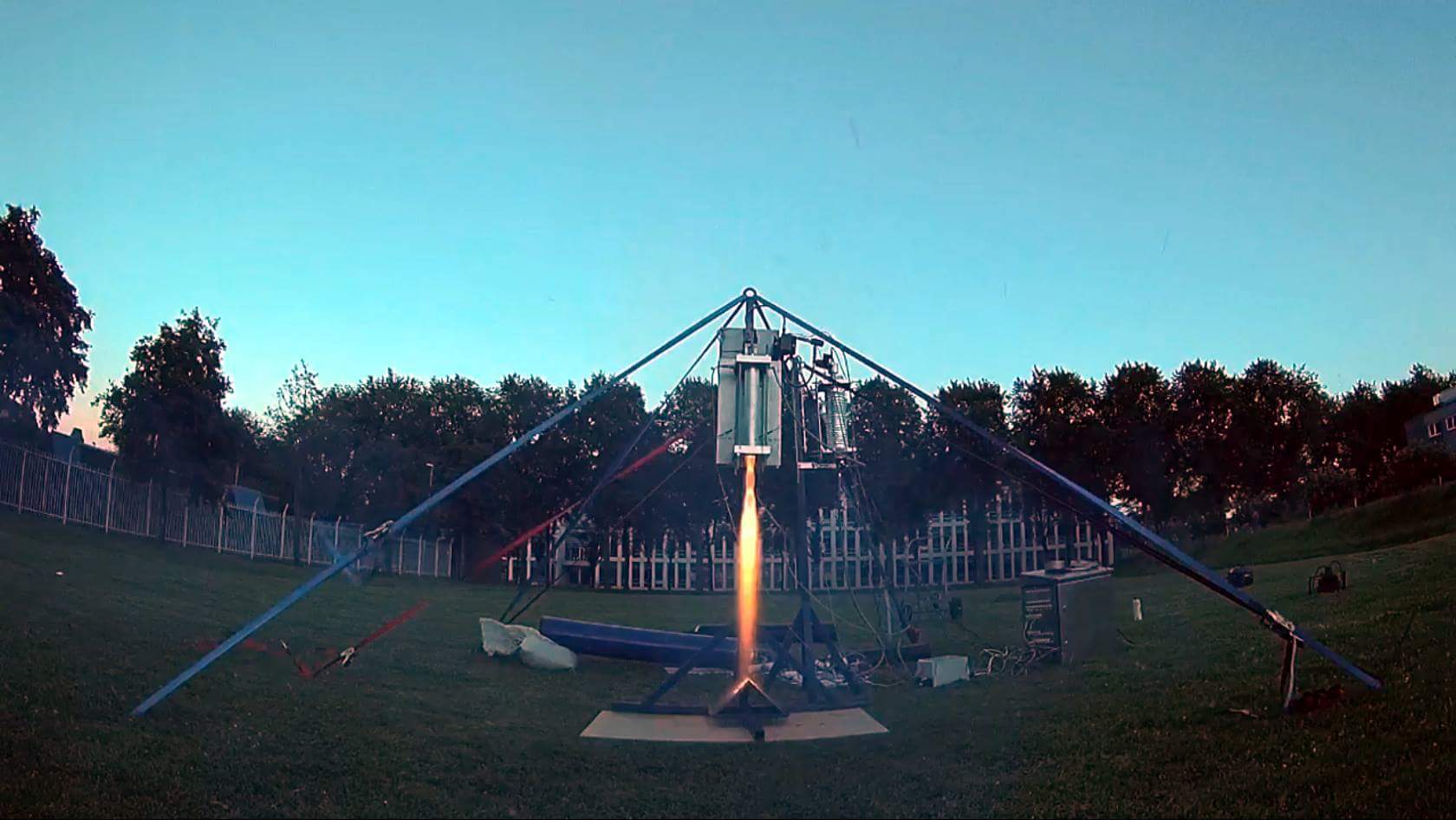
On the 20th of July Delft Aerospace Rocket Engineering tested its new Hybrid rocket engine: the DHX-4 Phoenix. The DHX-4 Phoenix is a relatively small engine with a thrust of around 1kN. The engine was designed to serve as a test bed for new technologies that can be used in a future Stratos-class engine. Besides serving as a test bed, the engine is also designed to be fully compatible with DARE’s CanSat V7 rocket. Last but not least, project Phoenix also provides an opportunity for some of the newer members within DARE to gain experience in designing and building hybrid rocket engines.
After the launch of Stratos II+, many of the veteran members of the hybrid propulsion team DAWN were graduating and leaving DARE. To ensure that the knowledge about Hybrid rocket engine technology within DARE was not lost, project Phoenix was initiated. The project Phoenix team consists of a mix of both older and newer DARE members to create an ideal learning environment. Project Phoenix is currently focused on the development of a 4kNs Hybrid rocket engine carrying the same name.
In December 2015 a critical design review was held within the society to get some valuable input on the design of the engine. After some small design changes the engine design was finalized and construction could start. In the same month, two versions of the oxidizer tank were constructed. These oxidizer tanks were pressure-tested at ALE in Delft until failure in order to validate the tank design. After two successful tests, the combustion chamber and the feed system of the engine were constructed in order to perform the first static fire tests. Besides constructing the engine, it was also required to upgrade the test bench used for the Morning star engine to accommodate the bigger DHX4-Phoenix. During the first weeks of July everything was ready and the first test campaign could start.
The first engine test was scheduled for the 9th of July. However, while setting up the engine on the field and testing the feed system, it was discovered that the main valve of the engine did not open as expected. Because of this it was decided to postpone the test to the 12th of July. On the 12th of July everything was ready and the whole test set up was assembled on the field. Because many the hybrid team members had already gone on vacation this was quite a challenge. After the set up was complete, a pressure test was performed and around 9 o’clock in the evening the engine was ready to be fired. After a thirty second countdown a big flame was expelled from the engine followed by a spray of white gas.
It was found that the igniter line, which supplies a small amount of nitrous oxide during the ignition, was not sufficiently choked leading to an abundance of oxidizer during the ignition sequence. The resulting pressure build up in the combustion chamber lead to the igniter being blown out of the combustion chamber and therefore ignition did not occur. Although the engine did not perform as expected, the team was happy to have successfully performed the whole test procedure and in the excitement it was quickly decided to do another test.
After redesigning the igniter mount and making some adjustments to the feed system, the engine was ready to be fired again on July the 20th. During leak testing of the set-up, it was discovered that the main valve was leaking. It was quickly found out that the off the shelf ball valve was the root cause of this leak. The test was postponed by two hours in order to replace this ball valve and adjust the set-up for the new valve. After fixing this problem, the team could start with the filling procedure and eventually the firing sequence.
During the firing sequence the ignition valve opened at T -3s to prime the chamber with N2O, followed by the ignition using a black powder igniter at T -2s. At T 0 the main valve opened releasing the full power of the DHX-4 Phoenix engine. The burn had a duration of around 4 seconds in nominal thrust conditions, afterwards the engine burned in a oxidizer rich condition for another 2 seconds. This was mainly due to filling the tank with too much oxidizer. Figures 1 and 2 present the thrust curve and the pressure graphs of the engine, respectively. The engine had a peak thrust of 877N and an average thrust of 680N, burning with an average ISP of 138s over the nominal burn phase. The chamber pressure was 28.3 Bar on average, which was a little lower than expected. Furthermore, the pressure drop across the injector was around 7.9 bar, which was significantly lower than anticipated.

Figure 2: Tank pressure, injector manifold pressure and combustion chamber pressure for the DHX4-Phoenix
The team is currently checking all the calculations and the test set-up again in order to identify the reasons for the under-performance. There are new tests planned with a shorter burn time in order to measure the ISP, regression rate and other engine performance parameters more accurately. Furthermore the team is looking into changing several design parameters in order to achieve the required performance. Follow us on YouTube and twitter if you want to be kept posted with the latest updates!